FIBRAS SINTETICAS
Este blog es un apoyo escolar que complementa lo visto en clase plasmándolo en esa base digital, con en fin de compartir lo relacionado a las fibras sintéticas.
22 may 2013
Spandex
Elastano (spandex)
Antecedentes
El spandex o elastano (en inglés elastane) es una fibra sintética conocida por su excepcional elasticidad. Es fuerte, pero menos duradero que su principal competidor no sintético, el látex natural. Se trata de un copolímero uretano-urea que fue inventado en 1959 por los químicos C.L. Sandquist y Joseph Shivers en Benger Laboratory de DuPont en Waynesboro, Virginia. Cuando se introdujo por primera vez, significó una revolución en muchos ámbitos de la industria textil.
El nombre de "spandex" es un anagrama del vocablo inglés "expands" (expandir). Es el nombre preferido en América del Norte; en Europa continental se denomina por variantes de "elastane", por ejemplo: Elasthanne (Francia), elastan (Alemania), elastano (España y Portugual), elastam (Italia) y Elasthaan (Holanda), y es conocido en el Reino Unido e Irlanda principalmente como Lycra. Los nombres del spandex incluida Lycra (hecho por la filial Koch Invista, previamente una parte de DuPont), Elaspan (también Invista), Acepora (Taekwang), Creora (Hyosung), ROICA y Dorlastan (Asahi Kasei), Linel (Fillattice), y ESPA (Toyobo).
![]() |
Ropa y prendas de vestir confeccionadas con spandex y otras fibras |

Al principio, su objetivo era desarrollar una hebra durable elástica a base de polímeros sintéticos. En 1940, los primeros elastómeros de poliuretano fueron producidos. Estos polímeros producidos eran elásticos, los cuales eran una alternativa adecuada a la goma. Aproximadamente al mismo tiempo, los científicos de Du Pont produjeron los primeros polímeros de nylon. Estos tempranos polímeros de nylon eran duros y rígidos, por lo que los esfuerzos habían comenzado por hacerlos más elástica. Cuando los científicos descubrieron que otros poliuretanos podría convertirse en hilos finos, se decidió que estos materiales podían ser útiles en la fabricación de medias de nylon estirables o utilizarlos en la fabricación de prendas de vestir de peso ligero.
Las primeras fibras spandex se produjeron a nivel experimental por uno de los pioneros de la química de polímeros, Farbenfabriken Bayer, obteniendo una patente alemana para su síntesis en 1952. El desarrollo final de las fibras se trabajó de forma independiente por los científicos de Du Pont y de Rubber Company EE.UU. Du Pont usó el nombre de Lycra y comenzó la fabricación a gran escala en 1962. Es actualmente el líder mundial en la producción de fibras spandex.

Síntesis y estructura química
Una gran variedad de materias primas se utilizan para producir fibras spandex. Esto incluye prepolímeros que producen la columna vertebral de la fibra, estabilizantes que protegen la integridad del polímero, y colorantes.Dos tipos de prepolímeros se hacen reaccionar para producir el polímero de la fibra spandex. Uno de ellos es un macroglicol flexible, mientras que el otro es un diisocianato rígido. El macro-glicol puede ser un poliéster, poliéter, policarbonato, policaprolactona o alguna combinación de estos. Estos son polímeros de cadena larga, que tienen grupos hidroxilo (-OH) en ambos extremos. La característica importante de estas moléculas es que son largas y flexibles. Esta parte de la fibra de spandex es responsable de su característica de estiramiento. El otro prepolímero que se utilice para producir spandex es un diisocianato polimérico. Este es un polímero de cadena más corta, que tiene un grupo isocianato (-NCO) en ambos extremos. La característica principal de esta molécula es su rigidez. En la fibra, esta molécula proporciona fuerza.
La estructura química del spandex es aproximadamente la siguiente:
![]() |
Estructura química del spandex |
Tiene enlaces urea y uretano en su cadena. Lo que le confiere al spandex sus características especiales, es el hecho de que en su estructura tiene bloques rígidos y flexibles. La cadena polimérica corta de un poliglicol, de generalmente cerca de cuarenta unidades de longitud, es flexible y parecida al caucho. El resto de la unidad de repetición, es decir el estiramiento con los enlaces uretano, los enlaces urea y los grupos aromáticos, es extremadamente rígido. Esta sección es tan fuerte que las secciones rígidas de diversas cadenas se agrupan y se alinean para formar fibras. Los dominios fibrosos formados por los bloques rígidos están unidos entre sí por las secciones flexibles parecidas al caucho. El resultado es una fibra que actúa como elastómero. Esto permite que logremos una tela capaz se estirarse, ideal para la ropa de gimnasia y similares.
Cuando los dos tipos de prepolímeros se mezclan entre sí, interactúan para formar las fibras de spandex. En esta reacción, los grupos hidroxilo (-OH) en los macroglicoles reaccionan con los isocianatos. Cada molécula se añade al final de otra molécula, y se forma un polímero de cadena larga. Esto se conoce como una polimerización por crecimiento en etapas o de adición. Para iniciar esta reacción, debe ser utilizado un catalizador tal como diazobiciclo(2.2.2)octano. Otras aminas de bajo peso molecular se añaden para controlar el peso molecular de las fibras.
Aditivos
Las fibras de spandex son vulnerables al daño de una variedad de fuentes, incluyendo calor, la luz, contaminantes atmosféricos y cloro. Por esta razón, se añaden estabilizantes para proteger las fibras. Los antioxidantes son un tipo de estabilizador.
Varios antioxidantes se añaden a las fibras, incluyendo fenoles impedidos monoméricos y poliméricos. Para proteger contra la degradación por luz, se añaden protectores contra los rayos ultravioleta (UV) tales como hidroxibenzotriazoles. Los compuestos que inhiben la decoloración de la fibra causada por los contaminantes atmosféricos son otro tipo de estabilizador añadido. Estos son típicamente compuestos con funcionalidad de amina terciaria, que pueden interactuar con los óxidos de nitrógeno en la contaminación del aire. Como el spandex se utiliza a menudo para trajes de baño, deben ser agregados aditivos fungicidas. Todos los estabilizadores que se añaden a las fibras de spandex están diseñados para ser resistentes a la exposición a disolventes ya que esto podría tener un efecto perjudicial sobre la fibra.
Las fibras de spandex son de color blanco. Por lo tanto, los colorantes se añaden para mejorar su apariencia estética. Típicamente se utilizan dispersantes y colorantes ácidos. Si las fibras de spandex se entretejen con otras fibras, tales como nylon o poliéster, métodos especiales de hilatura son necesarios.
Cuando los dos tipos de prepolímeros se mezclan entre sí, interactúan para formar las fibras de spandex. En esta reacción, los grupos hidroxilo (-OH) en los macroglicoles reaccionan con los isocianatos. Cada molécula se añade al final de otra molécula, y se forma un polímero de cadena larga. Esto se conoce como una polimerización por crecimiento en etapas o de adición. Para iniciar esta reacción, debe ser utilizado un catalizador tal como diazobiciclo(2.2.2)octano. Otras aminas de bajo peso molecular se añaden para controlar el peso molecular de las fibras.
Aditivos
Las fibras de spandex son vulnerables al daño de una variedad de fuentes, incluyendo calor, la luz, contaminantes atmosféricos y cloro. Por esta razón, se añaden estabilizantes para proteger las fibras. Los antioxidantes son un tipo de estabilizador.
Varios antioxidantes se añaden a las fibras, incluyendo fenoles impedidos monoméricos y poliméricos. Para proteger contra la degradación por luz, se añaden protectores contra los rayos ultravioleta (UV) tales como hidroxibenzotriazoles. Los compuestos que inhiben la decoloración de la fibra causada por los contaminantes atmosféricos son otro tipo de estabilizador añadido. Estos son típicamente compuestos con funcionalidad de amina terciaria, que pueden interactuar con los óxidos de nitrógeno en la contaminación del aire. Como el spandex se utiliza a menudo para trajes de baño, deben ser agregados aditivos fungicidas. Todos los estabilizadores que se añaden a las fibras de spandex están diseñados para ser resistentes a la exposición a disolventes ya que esto podría tener un efecto perjudicial sobre la fibra.
Las fibras de spandex son de color blanco. Por lo tanto, los colorantes se añaden para mejorar su apariencia estética. Típicamente se utilizan dispersantes y colorantes ácidos. Si las fibras de spandex se entretejen con otras fibras, tales como nylon o poliéster, métodos especiales de hilatura son necesarios.
Producción de fibras
Las fibras de spandex son producidos en cuatro formas diferentes: extrusión en estado fundido, hilado por reacción, hilatura en seco e hilado en húmedo. Todos estos métodos incluyen la etapa inicial de la reacción de monómeros para producir un prepolímero. Una vez que el prepolímero se forma, se hace reaccionar adicionalmente de diversas maneras y prolongado para hacer las fibras. El método de hilado seco se usa para producir más del 90% de fibras de spandex del mundo.![]() |
Proceso de hilatura en seco |
Hilatura en seco
Paso 1: El primer paso es producir el prepolímero. Esto se hace mediante la mezcla de una macro glicol con un monómero diisocianato. Los dos compuestos se mezclan en un recipiente de reacción para producir un prepolímero. Una proporción típica de glicol - diisocianato es de 1:2.
Paso 2: El prepolímero se hace reaccionar adicionalmente con una cantidad igual de diamina. Esta reacción se conoce como reacción de extensión de cadena. La solución resultante se diluye con un disolvente para producir la solución de hilado. El disolvente ayuda a hacer la solución más delgada y una manipulación más fácil, y entonces puede ser bombeado a la célula de producción de fibra.
Paso 3: La solución de hilado se bombea en una célula cilíndrica hilatura donde se cura y se convierten en fibras. En esta celda, la solución de polímero se fuerza a través de una placa de metal llamada hilera o spinneret. Esto hace que la solución se alinee en hebras de polímero líquido. Como los hilos pasan a través de la célula, se calientan en presencia de un gas nitrógeno y disolvente. Este proceso hace que el polímero líquido reaccionar químicamente y formar hebras sólidas.
Paso 4: Cuando las fibras salen de la célula, una cantidad de hebras sólidas se agrupan para producir el espesor deseado. Cada fibra de spandex se compone de muchas pequeñas fibras individuales que se adhieren el uno al otro debido a la pegajosidad natural de su superficie.
Paso 5: Las fibras resultantes se tratan después con un agente de acabado que puede ser estearato de magnesio o de otro polímero poli(dimetil-siloxano). Este tratamiento evita la fusión de las fibras entre sí y ayuda en la fabricación de textiles. Las fibras son entonces transferidas a través de una serie de rodillos sobre un carrete. La velocidad de bobinado de todo el proceso puede estar alrededor de 300 a 500 millas (482,7 hasta 804,5 km) por minuto en función del espesor de las fibras.
Paso 1: El primer paso es producir el prepolímero. Esto se hace mediante la mezcla de una macro glicol con un monómero diisocianato. Los dos compuestos se mezclan en un recipiente de reacción para producir un prepolímero. Una proporción típica de glicol - diisocianato es de 1:2.
Paso 2: El prepolímero se hace reaccionar adicionalmente con una cantidad igual de diamina. Esta reacción se conoce como reacción de extensión de cadena. La solución resultante se diluye con un disolvente para producir la solución de hilado. El disolvente ayuda a hacer la solución más delgada y una manipulación más fácil, y entonces puede ser bombeado a la célula de producción de fibra.
Paso 3: La solución de hilado se bombea en una célula cilíndrica hilatura donde se cura y se convierten en fibras. En esta celda, la solución de polímero se fuerza a través de una placa de metal llamada hilera o spinneret. Esto hace que la solución se alinee en hebras de polímero líquido. Como los hilos pasan a través de la célula, se calientan en presencia de un gas nitrógeno y disolvente. Este proceso hace que el polímero líquido reaccionar químicamente y formar hebras sólidas.
Paso 4: Cuando las fibras salen de la célula, una cantidad de hebras sólidas se agrupan para producir el espesor deseado. Cada fibra de spandex se compone de muchas pequeñas fibras individuales que se adhieren el uno al otro debido a la pegajosidad natural de su superficie.
Paso 5: Las fibras resultantes se tratan después con un agente de acabado que puede ser estearato de magnesio o de otro polímero poli(dimetil-siloxano). Este tratamiento evita la fusión de las fibras entre sí y ayuda en la fabricación de textiles. Las fibras son entonces transferidas a través de una serie de rodillos sobre un carrete. La velocidad de bobinado de todo el proceso puede estar alrededor de 300 a 500 millas (482,7 hasta 804,5 km) por minuto en función del espesor de las fibras.
Paso 6: Cuando los carretes están llenos de fibra, se colocan en el embalaje final y es enviado a los fabricantes de textiles. Aquí, las fibras pueden ser tejidas con otras fibras tales como algodón o nylon para producir la tela que se utiliza en la fabricación de ropa. Esta tela también puede ser teñida para producir el color deseado.

![]() |
Carrete de spandex |
Principales usos
El spandex se utiliza para la confección de ropa y prendas de vestir donde la elasticidad es deseable, generalmente para comodidad y ajuste, tales como: ropa deportiva, cinturones, cintas de sujetador, traje de baño competitivo, pantalones cortos de ciclista, cinturones de baile usado por los bailarines masculinos y otros, guantes, calcetería, polainas, artículos ortopédicos, pantalones de esquí, jeans ajustados, pantalones, minifaldas, ropa interior, prendas de compresión tales como corsetería y trajes de captura de movimiento, prendas con forma tales como copas del sujetador entre tantos otros usos.Para la ropa, el spandex generalmente se mezcla con algodón o poliéster, y representa un pequeño porcentaje de la tela final, por lo tanto, el tejido final conserva la mayor parte de la apariencia de las otras fibras. Es de poco uso en ropa de hombre, pero frecuente en el de las mujeres. Se estima que un 80% de la ropa que se vende en los Estados Unidos contenía spandex en 2010.
![]() |
Short (95% Algodón y 5% elastano) |
![]() |
Remera surf (88% poliamida y 12% elastano) |
![]() |
Media de compresión (20% Elastano y 80% Poliamida) |
![]() |
Soporte para talón (Algodón 76%, Elastano 15%, Poliamida 9%)
|
Vista transversal

Polivinilo
Acetato de Polivinilo
Antecedentes
![]() |
Dr. Fritz Klatte |
ElLa síntesis de acetato de vinilo monómero fue patentado en Alemania por el Dr. Fritz Klatte en 1913. El poliacetato de vinilo, acetato de polivinilo, PVA, PVAc o poli (etenil etonoato), es un polímero sintético gomoso con fórmula abreviada (C4H6O2)n. Pertenece a la familia de los polímeros poliviníl éster más fácilmente obtenible y de más amplio uso, con fórmula general -(RCOOCHCH2)-. Se trata de un tipo de termoplástico. No se debe confundir con la relación del polímero alcohol polivinílico, que se lo denomina, en muchos casos, también con las siglas PVA (talvez PVAc podría considerarse como una abreviatura técnicamente correcta para el acetato de polivinilo y ayudaría a evitar una confusión de este tipo). El acetato de polivinilo es un componente de un tipo ampliamente usado de adhesivo, a que se refiere indistintamente como cola para madera, cola blanca, cola de carpintero, cola escolar, cola PVA o cola vinílica.
ESTRUCTURA QUÍMICA Y SÍNTESIS
La estructura química del polímero se compone sucesiones de grupos vinilacetato:El acetato de polivinilo es preparado por polimerización vinílica por radicales libres del monómero acetato de vinilo.

El monómero de acetato de vinilo, fue a escala industrial producido por primera vez por la adición de ácido acético al acetileno con una sal mercurio (I), pero ahora está compuesta principalmente por la adición oxidativa catalizado con paladio de ácido acético al etileno.
PROCESO DE FABRICACIÓN
En la industria de los adhesivos se obtiene el poliacetato de vinilo por los métodos convencionales de polimerización por adición o por emulsión.Para iniciar la polimerización es común activar la doble ligadura del vinilo ya sea termicamente, o fotoquímicamente por reacción con un radical libre iniciador o por reacción con un catalizador iónico. La polimerización de adición industrial para los adhesivos, se inician por lo general, por medio de un radical libre obtenido de la descomposición de agentes oxidantes tales como el peróxido de benceno. Simultáneamente la ligadura de vinilo es activada ya que ahora ella tiene un electrón sin unir en el otro átomo de carbono. Es así como se inicia una reacción en cadena de radicales libres.
El vinil acetato monómero puede ser copolimerizado o terpolimerizado con otros compuestos no saturados y, de esta manera, obtener sustancias poliméricas con diferencias en sus propiedades físicas tales como los sólidos suspendidos, viscosidad, plásticidad y características adhesivas del producto resultante.
El acetato de vinilo puede ser copolimerizado con varios monómeros de vinilo. Son comonómeros comercialmente importantes el cloruro de vinilo, cloruro de vinilideno, dibutilo y otros maleatos y fumaratos de dialquilo, los ácidos crotónicos, acrílico, metacrílico e itacónico y sus ésteres, pirrolidona y etileno de vinilo. Un monómero que no se combina sólo con el acetato de vinilo puede combinarse con el uso de un tercer monómero que se copolimeriza con ambos (terpolimerización). La injerción puede usarse con monómeros como el estireno, que no se copolimeriza con el acetato de vinilo.
ADHESIVOS DE POLIVINIL ACETATO
1. Polimerización del monómero vinil acetato (VAM). El proceso de polimerización se efectúa de la siguiente manera: Inicialmente se adiciona en el reactor de polimerización la solución del coloide protector (sustancia que ayuda a mantener las características de homogeneidad en un sistema polimérico), la cual se calienta a una temperatura promedio de 80ºC con el fin de mejorar la solubilidad del monómero de vinil acetato en el agua. Posteriormente se adiciona el o los monómeros, el catalizador y se da inicio a la agitación.
El calentamiento que se debe suministrar inicialmente en el reactor de polimerización se mantiene mediante una camisa de calentamiento, en donde se suministra vapor. La reacción de polimerización es exotérmica, por cuanto una vez iniciada la reacción es necesario retirar el vapor de la camisa y suministrar un suficiente volumen de agua de enfriamiento para mantener la temperatura de reacción, que dependiendo de la tecnología y capacidad de la planta puede variar de 65 a 80ºC.
Condiciones de operación en la etapa de polimerización.
Temperatura de reacción: En la industria el rango de temperatura varia de 65 a 80ºC.
Tiempo de reacción: 8-14 horas. El tiempo depende de factores tales como la temperatura de reacción y la agitación a la cual es sometida.
Volumen del agua de enfriamiento: 0.43 m3/h.Temperatura a la entrada del agua: 24ºC Temperatura del agua de salida: 35ºC.Para una planta en particular, donde se producen un número indefinido de formulaciones para adhesivos, se puede citar como propiedades típicas para del producto final de la polimerización, una viscosidad promedio de 22000 cps y un pH entre 4 y 5. El polímero es envasado en tambores y distribuido a las industrias de pegantes en donde se realiza la etapa de dilución del pegante.
Una vez el polímero ha sido hecho, probado y caracterizado, aún necesita ser sujeto a las pruebas de comportamiento adhesivo. La adhesión a superficies específicas; resistencia de la unión a envejecimiento temperaturas extremas, características de aplicación apropiadas y su economía son unas pocas de las consideraciones importantes.
2. Dilución y preparación de los pegantes de poliacetato de vinilo.Con frecuencia las emulsiones se pueden usar con alguna modificación alterando sus propiedades físicas tales como la viscosidad, elasticidad, porcentaje de sólidos y resistencia al agua, para variar características de aplicación tales como la pegajosidad y mecanibilidad, además de reducir los costos de producción de los pegantes, por cuanto se disminuye el consumo de la emulsión.
Es importante conocer el pH y el tipo de coloide protector o emulsificante, con el fin de seleccionar los ingredientes o aditivos modificadores de la emulsión. El pH y el tipo de emulsificante también pueden afectar la aplicación y la fuerza de la unión cuando los adhesivos son aplicados en ciertos tipos de adherentes reactivos.
Los almidones, las soluciones de alcohol polivinilico (PVOH) y las arcillas son agentes reductores de costo. Los almidones proveen una alta viscosidad. El alcohol polivinílico forma viscosidad, mejora la mecanibilidad y la resistencia al agua. Las arcillas mejoran las propiedades de fraguado al controlar la penetración en sustratos porosos.
El rápido fraguado mejorado y las características de pegajosidad se alcanzan con la adición de plastificantes, solventes y agentes de colascencia de la película. También facilitan la velocidad de fraguado al aumentar el contenido de sólidos.
El poliacetato de vinilo y el alcohol polivinílico son materias primas importantes para adhesivos de maderas, al ofrecer gran fuerza de unión, rápido fraguado, tiempos de montaje abiertos y cerrados controlables, líneas de cola incoloras y fácil aplicación a temperatura ambiente.
La operación de dilución consiste en adicionar, a una cantidad determinada de emulsión de poliacetato de vinilo, el espesante y/o plastificante requerido y agitar por un tiempo aproximado de una hora a temperatura ambiente.
Las emulsiones adhesivas de polivinil acetato ofrecen una rápida pegajosidad, buena adhesión a muchas superficies, resistencia a la grasa, además de ser una sustancia no tóxica.
El reactor de polimerización son recipientes herméticamente cerrado, para evitar posibles fugas de los monómeros, disponen de un agitador con eje en el centro del recipiente, control de temperatura y presión. La capacidad del tanque varía de acuerdo a la capacidad instalada de la planta.
EMULSIONES DE POLIVINIL ACETATO
El polivinil acetato es ampliamente utilizado en la forma de una dispersión de resina sólida en agua. Se producen éstas dispersiones por medio del proceso de polimerización por emulsión.
La mayoría de los manufactureros especifican las propiedades de sus emulsiones las que ordinariamente incluyen: porcentaje de sólidos, viscosidad de la emulsión, pH, contenido de ácido, porcentaje de monómero sin reaccionar y densidad. Ocasionalmente se destacan otras propiedades como el tamaño de partícula, propiedades de la película del adhesivo tales como claridad, resistencia al agua y la grasa, y la tolerancia de la emulsión hacia productos químicos orgánicos o inorgánicos.
![]() |
TABLA Adhesivos de Acetato de Polivinilo |
Los principales tipos de emulsiones de polivinil acetato que comúnmente se encuentran en el mercado pueden clasificarse de la siguiente manera:
- Clase I: Emulsiones de homopolímeros para uso general. Tienen tamaño de partícula y peso molecular heterogéneos. Son estables al almacenamiento y manejo. El coloide protector (sustancia que ayuda a mantener las características de homogeneidad en un sistema poliméricos) usualmente es el alcohol polivinilico. Su viscosidad varia de 4000 a 5000 cps, el contenido de sólidos generalmente es de 55 % y el pH de 4 a 5. Estas emulsiones son altamente compatibles con plastificantes, agentes humectantes, espesadores y otros agentes modificadores facilitando así la transformación rápida hacia una variedad de adhesivos.
- Clase II: Emulsiones homopolímeras para usos especiales. Son similares a la de la clase I, pero les falta un amplio margen de compatibilidad con los agentes modificadores; ésta propiedad se ve disminuida para conservar otras propiedades especiales de la emulsión como son: un alto peso molecular para un mayor agarre a altas temperaturas, un tamaño de partícula grueso para un mayor agarre en superficies porosas, o un peso molecular bajo para un rápido agarre. El tamaño de partículas de las emulsiones de la clase I y II promedian entre 0.5 a 10 micrones.
- Clase III: Emulsiones de homopolímero de película libre. Forman películas libremente a la temperatura ambiente, que permanecen en presencia de agua sin necesidad de agregar agentes coalescentes a las emulsiones. Estas emulsiones tienen un tamaño de partícula más fina y uniforme que las emulsiones de las clases I y II, el tamaño varía entre 0.45 a 1 o 2 micrones.
La mayoría de las emulsiones de la clase III se hacen por un proceso de adición gradual de monómero para controlar el tamaño de partícula y el peso molecular; se usa un surfactante para obtener partículas más chicas y más uniformes. La cantidad de coloide protector se reduce a menos de la mitad del usado para hacer los productos de la clase I y II para mejorar las propiedades de película libre.
En ésta clase es útil hacer una subdivisión de acuerdo con el tipo de emulsificante o coloide protector utilizado.
PROPIEDADES
El grado de polimerización de acetato de polivinilo normalmente es de 100 a 5000. Los grupos éster del acetato de polivinilo son estables en sistemas neutros, pero son sensibles a los álcalis y poco a poco convertirán el PVAc en alcohol polivinílico y ácido acético.
El poliacetato de vinilo es demasiado blando y tiene una excesiva fluencia en frio debido a que su temperatura de transición vítrea es de 28°C, muy próxima a la temperatura ambiente. La densidad es de 1,19g/cm3 y su índice de refracción 1,47. Es atáctico y no cristaliza (amorfo). Los polímeros estereorregulares no se han ofrecido comercialmente. Es transparente si está libre de emulsificante. Su parámetro de solubilidad, d=19,4(MJ/m3)0,5; lo disuelven el benceno (d=18,8) y la acetona (20,4)
Los polímeros de bajo peso molecular son frágiles pero se hacen como goma cuando se mastican y de hecho se utilizan en las gomas de mascar.
APLICACIONES Y USOS
Es usado generalmente para adhesivos de encuadernación, bolsas de papel, cartones para leche, sobres, cintas engomadas, calcomanías, etc. Existen grados alimenticios utilizados como aditivo para alimentos. También es materia prima para la producción de otros polímeros.
Adhesivos: El poliacetato de vinilo es de uso extendido en adhesivos, tanto del tipo emulsión como del de fusión en caliente (hot melt)
En emulsión acuosa, el PVAc se utiliza como adhesivo para materiales porosos, en especial para madera, papel y tela.
Recubrimiento y aglutinante: El homopolímero PVAc, pero sobre todo el copolímero, combinación de acetato de vinilo y etileno (etileno acetato de vinilo o VAE), se utiliza también en el recubrimiento de papel, pinturas y otros recubrimientos industriales, como aglutinante en telas no tejidas de fibra de vidrio, toallas sanitarias , papel de filtro y en acabado textil. También se utiliza como aditivo para el concreto.
Una aplicación interesante es el uso de una emulsión de PVA para aumentar la adherencia entre el concreto viejo y el nuevo. Hay dos formas en que esto se puede hacer, ya sea cubriendo el concreto viejo antes de aplicar la mezcla de cemento, o la mezcla una proporción de la emulsión de PVA con la nueva mezcla.
En alimentos: El PVAc también puede ser utilizado como recubrimiento para proteger el queso de los hongos y la humedad. Se usa como base de plástico neutro para la goma de mascar ya que es un sustituto barato de la savia gomosa natural del árbol Manilkara zapota.
En la industria farmacéutica, el acetato de vinilo copolimerizado con vinilpirrolidona, poli(vinilpirrolidona-co-vinilacetato), también es utilizado como excipiente en algunos comprimidos.
Base para otros polímeros El acetato de polivinilo es también la materia prima para hacer otros polímeros como:
- Alcohol de polivinilo -[HOCHCH2]-: acetato de polivinilo es parcial o completamente hidrolizado para dar el alcohol polivinílico. El polivinil acetato parcialmente hidrolizado con NaOH y metanol da un copolímero de poli (alcohol vinílico-co-vinil acetato). Esta reacción se controla para dar un 20% de grupos acetato en el polímero. El poli (alcohol vinílico-co-vinil acetato) es utilizado en pinturas acrílicas para crear una suspensión de PMMA en agua puesto que presenta partes polares y no polares. A estas pinturas se las denomina pinturas al látex (pinturas en emulsión acuosa).
- Copolímeros: El poliacetato de vinilo se copolimeriza frecuentemente con dimetil fumarato, vinil estereato, 2-etilhexil acrilato o etil acrilato, o se plastifica, para obtener composiciones más blandas para su uso en emulsiones.
- Ftalato de acetato de polivinilo (PVAP): El acetato de polivinilo parcialmente hidrolizado y esterificado con ácido ftálico .
Adhesivos: El poliacetato de vinilo es de uso extendido en adhesivos, tanto del tipo emulsión como del de fusión en caliente (hot melt)
En emulsión acuosa, el PVAc se utiliza como adhesivo para materiales porosos, en especial para madera, papel y tela.
![]() |
Adhesivo para madera |
Recubrimiento y aglutinante: El homopolímero PVAc, pero sobre todo el copolímero, combinación de acetato de vinilo y etileno (etileno acetato de vinilo o VAE), se utiliza también en el recubrimiento de papel, pinturas y otros recubrimientos industriales, como aglutinante en telas no tejidas de fibra de vidrio, toallas sanitarias , papel de filtro y en acabado textil. También se utiliza como aditivo para el concreto.
Una aplicación interesante es el uso de una emulsión de PVA para aumentar la adherencia entre el concreto viejo y el nuevo. Hay dos formas en que esto se puede hacer, ya sea cubriendo el concreto viejo antes de aplicar la mezcla de cemento, o la mezcla una proporción de la emulsión de PVA con la nueva mezcla.
En alimentos: El PVAc también puede ser utilizado como recubrimiento para proteger el queso de los hongos y la humedad. Se usa como base de plástico neutro para la goma de mascar ya que es un sustituto barato de la savia gomosa natural del árbol Manilkara zapota.
![]() |
Goma de mascar |
![]() |
Comprimidos de Hidroxil (Excipientes: Copolímero polivinilpirrolidona-polivinil acetato 60/40) |
Base para otros polímeros El acetato de polivinilo es también la materia prima para hacer otros polímeros como:
- Alcohol de polivinilo -[HOCHCH2]-: acetato de polivinilo es parcial o completamente hidrolizado para dar el alcohol polivinílico. El polivinil acetato parcialmente hidrolizado con NaOH y metanol da un copolímero de poli (alcohol vinílico-co-vinil acetato). Esta reacción se controla para dar un 20% de grupos acetato en el polímero. El poli (alcohol vinílico-co-vinil acetato) es utilizado en pinturas acrílicas para crear una suspensión de PMMA en agua puesto que presenta partes polares y no polares. A estas pinturas se las denomina pinturas al látex (pinturas en emulsión acuosa).
- Copolímeros: El poliacetato de vinilo se copolimeriza frecuentemente con dimetil fumarato, vinil estereato, 2-etilhexil acrilato o etil acrilato, o se plastifica, para obtener composiciones más blandas para su uso en emulsiones.
- Ftalato de acetato de polivinilo (PVAP): El acetato de polivinilo parcialmente hidrolizado y esterificado con ácido ftálico .
Poliuretano
Poliuretano
ANTECEDENTES
1937 Otto Bayer inventor del poliuretano |
En 1937 el médico Otto Bayer estaba buscando una nueva ruta para sintetizar fibras que, después de la invención del nylon, había aumentado la demanda de fibras sintéticas para sustituir a la seda. Con 35 años de edad, con el entonces jefe del laboratorio científico principal de la designadaIG Farben en Leverkusen (Alemania), no sólo interesa a desarrollar un nuevo producto químico, pero también pretende conseguir un método de producción de plásticos más simples y con menos subproductos.
Su invención de los productos químicos de poliuretano (PUR), basado en la reacción de diisocianatos y polioles, implantado sin ningún esfuerzo: la idea de plástico sintetizar a partir de los isocianatos, conocidos por su alta reactividad e inestabilidad química, no era muy recibido por su parte superior. A pesar de ello, el 13 de noviembre 1937 solicitó una patente en los resultados de la investigación y se puede considerar que la patente imperial alemana DRP 728.981 constituye la «partida de nacimiento» de los productos químicos del poliuretano.
La década de 1940: el trabajo pionero de químicos e ingenieros
Simultáneamente a los trabajos de laboratorio, el inventor y su equipo dedican a dilucidar dónde podrían aplicarse las espumas, fibras y elastómeros del nuevo plástico. Algunas citas de las patentes básicas registradas hasta 1948 muestran que los investigadores desarrollaron una enorme creatividad: "Los materiales porosos ligeros se adaptan como el material de apoyo en la construcción de aviones y barcos, como aislante térmico y acústico, para piezas de muebles, ruedas , juguetes, construcción de edificios, prótesis, suelas de calzado y vendajes de tracción ".
![]() |
La estación de carga para los vehículos eléctricos. |
La década de 1950: evolución y primeros lanzamientos al mercado
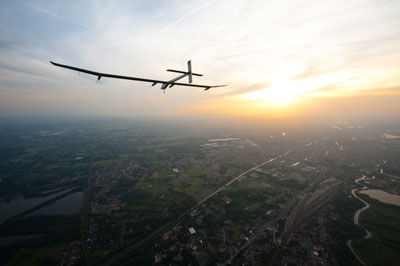
En 1955 Bayer registra la marca Desmopan para su poliuretanos termoplásticos (TPU)-poliuretanos por su origen químico y termoplástico por su proceso de transformación-, algunos productos versátiles que ofrecer un amplio espectro de posibilidades de uso. Desde 1958, las pinturas de poliuretano a la base de Desmodur y Desmophen (pinturas DD) se convirtió en sinónimo de pinturas de alto rendimiento para la reparación de vehículos, barcos y aviones.
La década de 1960: las espumas rígidas y flexibles conquistar el mercado
El año 1960 marca el logro de un nuevo hito en la historia de la PUR: en este año se presenta por primera vez una espuma rígida con capas metálicas superpuestas, lo que hoy se conoce como paneles metálicos tipo sándwich. Las espumas flexibles, por su parte, conquistan los muebles y las sillas de los camiones al ofrecer confort y un alto grado de higiene.
Esta década también marcó el primer uso de las espumas integrales de poliuretano en la fabricación de reposabrazos para los camiones. Los productos fabricados a partir de este material de caracterizan por una transición continua y gradual, a partir de una superficie lisa hasta que un núcleo celular, de manera similar a la estructura de los huesos. Al año siguiente nace el elastómero de extraordinaria Vulkollan disposición, capaces de resistir las condiciones más extremas, como en su uso en las ruedas de carretillas elevadoras.
![]() |
Plato de ducha. |
A la vista de estos grandes avances no es de extrañar que también el consumo de PUR aumento de forma exponencial. Sólo durante los 'años 60 vibrantes de los mundiales aumenta la producción anual de las 200.000 toneladas a más de 500.000. Este es también el período en el que ya está en el mercado en todo el espectro de componentes de poliuretano: a partir de los diisocianatos que van a través de los distintos tipos de polioles, catalizadores y espumantes, hasta que los aditivos para los fines más diversos.
La década de 1970: el poliuretano se convierte en parte integral de la vida diaria
Las dos crisis del petróleo de la década de 1970 el crecimiento de freno del consumo de poliuretano, aunque no repercuten sobre una base a largo plazo en la evolución del consumo, como los poliuretanos ya se han convertido en parte integrante de numerosos campos, desde los sectores del automóvil y de la construcción, pasando a través de la la industria textil y la alimentación hasta que el sector de la salud. Se lanzan nuevos productos al mercado, con lo que volver a incrementar las posibilidades de negocio. Un ejemplo de esto es el espumado de cavidades en los camiones.
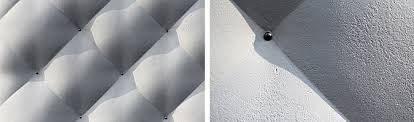
Otro de los resultados de la cooperación entre los químicos e ingenieros fue la introducción en 1971 de que el técnico del moldeo por inyección con reacción (RIM) que permite, por medio de la introducción de los componentes reactivos de PUR a alta presión en un molde, los fabricación de grandes piezas en ciclos breves y de alta calidad reproducible. Así, en la actualidad se fabrican en un solo suceden grandes piezas de carrocería de varios metros cuadrados de superficie para la maquinaria agrícola.
La década de 1980: expansión gracias a la innovación y las ideas sostenibles
Las propiedades a medida de los clientes del poliuretano ganan cada vez más importancia. Un ejemplo lo constituye el aumento del confort y la funcionalidad de los asientos de los camiones en los que ahora se combinan dos durezas diferentes. Gracias al sistema de PUR Bayfit de Bayer y de la cabezales mezcladores multicomponente, es posible fabricar dichos asientos en una sola operación.
Para finales de la década de 1980 el lanzamiento al mercado de la materia prima y Bayhydrol Bayhydur para pinturas acuosas gotas de disolvente. Otra novedad es la introducción sostenible de espumas flexibles fabricadas sin clorofluorocarbonos (CFC), un proceso más respetuoso con el medio ambiente. En la actualidad los poliuretanos también contribuyen en mayor medida a la higiene de los clientes finales: así, en los habitáculos de los camiones, las espumas absorbentes de energía fabricados con Bayfill EA proteger a los ocupantes del vehículo en caso de choques laterales.
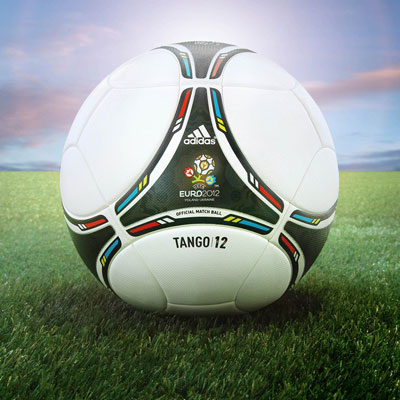
Balloon Eurocopa - Tango 12.
La década de 1990: una mayor proximidad al cliente y un servicio más
Esta década se caracteriza por la expansión global del poliuretano. Al mismo tiempo, empresas como Bayer crear redes mundiales de centros de asesoramiento, distribución y servicio técnico de apoyo de préstamos a los clientes y que éstos abastecerse flexibles y rápidos.
Un hito fue la introducción de las espumas viscoelásticas, que caracterizan a la recuperación de forma muy lenta a su forma inicial, que ofrece una gran capacidad de adaptación y mayor confort que las espumas flexibles convencionales. Un campo importante de aplicación son los colchones para los pacientes postrados que advierten al aprendizaje de las úlceras por presión.
El siglo 21: sigue el camino de los éxitos
Con el desarrollo de los sistemas de pulverización de PUR Baypreg y Multitec, Bayer MaterialScience inicia el nuevo milenio, abriendo la puerta a una nueva clase de materiales compuestos que combinan un bajo peso con una elevada rigidez, y que ofrece numerosas posibilidades de aplicación, desde la camiones a los dispositivos sanitarios.

Las grandes tendencias globales, como el cambio climático, se plantean nuevos retos tanto en el campo del aislamiento térmico de los edificios y de la cadena del frío, como en el de la fabricación de camiones ligeros que funcionan de forma eficiente y preservar los recursos naturales. Bayer MaterialScience busca soluciones para estas grandes tendencias y presentó algunas novedades a este respecto en el marco de la feria Utech 2012 como, por ejemplo, un sistema de espuma rígida de la cadena del frío con el que logra un mayor aislamiento y un material más ligero para la fabricación de piezas de camiones. Además, también se están abriendo perspectivas totalmente nuevas para la fabricación ecológica de las materias primas de PUR a partir del gas de efecto invernadero CO 2 . Estos datos hacen prever que la buena trayectoria de los poliuretanos se mantendrá también en el siglo 21.
Propiedades
- La mayoría de los poliuretanos son termoestables aunque existen algunos poliuretanos termoplásticos para algunas aplicaciones especiales.
- Posee un coeficiente de transmisión de calor muy bajo, mejor que el de los aislantes tradicionales, lo cual permite usar espesores mucho menores en aislaciones equivalentes.
- Mediante equipos apropiados se realiza su aplicación "in situ" lo cual permite una rápida ejecución de la obra consiguiéndose una capa de aislación continua, sin juntas ni puentes térmicos.
- Su duración, debidamente protegida, es indefinida.
- Tiene una excelente adherencia a los materiales normalmente usados en la construcción sin necesidad de adherentes de ninguna especie.
- Tiene una alta resistencia a la absorción de agua.
- Muy buena estabilidad dimensional entre rangos de temperatura desde -200 ºC a 100 ºC.
- Refuerza y protege a la superficie aislada.
- Dificulta el crecimiento de hongos y bacterias.
- Tiene muy buena resistencia al ataque de ácidos, álcalis, agua dulce y salada, hidrocarburos, etc.
Propiedades físicas
Aunque es evidente que las propiedades físicas dependen mucho del proceso de fabricación aquí hay ejemplos de ciertos compuestos.
Densidad
|
D-1622
|
Kg./m3
|
32
|
40
|
48
|
Resistencia Compresión
|
D-1621
|
Kg./cm2
|
1.7
|
3.0
|
3.5
|
Módulo compresión
|
D-1621
|
Kg./cm2
|
50
|
65
|
100
|
Resist. Tracción
|
D-1623
|
Kg./cm2
|
2.5
|
4.5
|
6
|
Resist. Cizallamiento
|
C-273
|
Kg./cm2
|
1.5
|
2.5
|
3
|
Coef Conductividad
|
C-177
|
Kcal/m.hºC
|
0.015
|
0.017
|
0.02
|
Celdas cerradas
|
D-1940
|
%
|
90/95
|
90/95
|
90/95
|
Absorción de agua
|
D-2842
|
g/m2
|
520
|
490
|
450
|
Propiedades mecánicas
Las propiedades mecánicas dependen de la medida de su peso volumétrico; a medida que este aumenta, aumenta su propiedad de resistencia. Los pesos volumétricos más usuales se hallan comprendidos entre 30 y 100 kg/m3, dentro de estos límites se obtienen los siguientes valores:- Resistencia a la tracción entre 3 y 10 (Kp./cm2)
- Resistencia a la compresión entre 1,5 y 9 (Kp./cm2)
- Resistencia al cizallamiento entre 1 y 5 (Kp./cm2)
- Módulo de elasticidad entre 40 y 200 (Kp./cm2)
Resistencia a los productos químicos
El poliuretano es resistente al agua potable, al agua de lluvia y al agua de mar, las soluciones alcalinas diluidas, los ácidos diluidos, los hidrocarburos alifáticos como por ejemplo la gasolina normal, el carburante diesel, el propano, el aceite mineral, así como los gases de escape y el aire industrial (SO2). Es condicionalmente resistente (hinchamiento o encogimiento) a los siguientes productos: los hidrocarburos clorados, las acetonas y los éteres, no es resistente a los ácidos concentrados.Poder adhesivo
Una propiedad particularmente interesante del poliuretano es para el empleo como material de construcción por su adhesión a diferentes materiales. Durante la fabricación la mezcla experimenta su estado intermedio pegajoso y en virtud de la fuerza adhesiva propia, automática y excelentemente se adhiere al papel, al cartón y al cartón asfaltado para techos, así como a las maderas, a las planchas de fibras duras y de virutas prensadas, a la piedra, al hormigón, al fibrocemento, a las superficies metálicas y a un gran número de materias plásticas.Los poliuretanos tienen en general las siguientes características:
- excelente tenacidad.
- flexibilidad, alta capacidad de alargamiento.
- excelente relleno de holgura.
- puede pintarse una vez curado.
- excelente resistencia química.
Suscribirse a:
Entradas (Atom)